A M2J Engenharia está participando, em conjunto com as empresas CRI Gestão de Resíduos e…
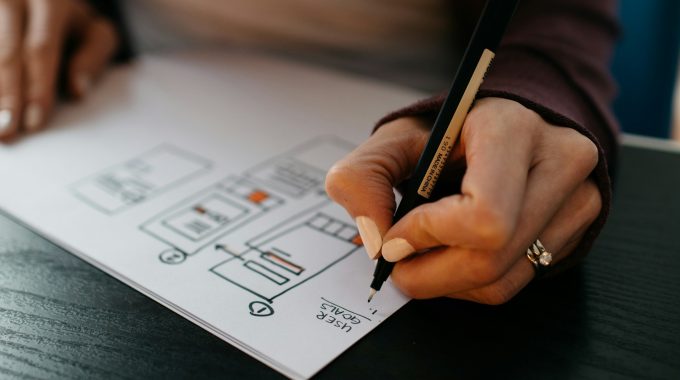
Metodologia Lean: aumento de eficiência e produtividade
Muitas empresas enfrentam diariamente o desafio de gerar resultados com baixos investimentos, aproveitando ao máximo o conhecimento da equipe. Uma maneira eficiente de fazer isso é por meio da implementação da metodologia Lean, pois trata-se de uma abordagem que permite enxergar os processos de forma diferente e também identificar e realizar melhorias — os chamados kaizens.
O que é a metodologia Lean Thinking?
O Lean Thinking, traduzido como “pensamento enxuto”, é uma maneira de pensar e atuar com o objetivo de otimizar processos. Ele tem como base o Sistema Toyota de Produção, e foca principalmente na redução dos sete desperdícios.
Mas, antes de continuar, é importante entender: o que são desperdícios?
Os 7 principais desperdícios considerados pela metodologia Lean Thinking
Desperdícios são todas as atividades que não agregam valor ao cliente, ou seja, aquilo pelo qual o cliente não está disposto a pagar. Esses desperdícios geram custos extras e não contribuem para transformar insumos em produtos. Os principais são:
- Transportes desnecessários de materiais: Quando o material é movimentado de um lugar para outro. Nesse caso, estamos acostumados com essa movimentação, e acreditamos ser parte inerente do fluxo. Entretanto, muitas vezes é fácil de ser reduzido ou eliminado.
- Espera: Quando os colaboradores precisam aguardar, seja por manutenção de máquinas, troca de produção ou pela chegada de insumos que ainda não estão na linha.
- Movimentação desnecessária de pessoas: Isso inclui busca por padrões, informações, liberações e aprovações.
- Perdas: Este é o desperdício mais visível. Muitas vezes é o primeiro a ser lembrado, mas não necessariamente o mais relevante. Depende da situação e da quantidade em questão.
- Superprodução: Produzir mais do que o necessário, seja produto final ou intermediário. Este é considerado o pior desperdício, pois pode causar rupturas de materiais. Já vivenciou a situação em que um insumo foi utilizado em uma produção que ultrapassou o programado, gerando falta desse mesmo insumo para outro item onde ele também era necessário? Esse tipo de problema ilustra bem o impacto da superprodução.
- Superprocessamento: Realizar atividades que consomem mais energia, tempo ou outros recursos sem necessidade. Por exemplo, imagine um processo de congelamento em que o padrão seria o produto atingir -12ºC, mas ele é congelado até -20ºC. O cliente “paga” pelo padrão de -12ºC, e o excedente de resfriamento até -20ºC, apenas consome mais energia, sem agregar valor.
- Estoques desnecessários: Muitas vezes ouvimos a frase “Lean é estoque zero”. Na verdade, o ideal é ter o estoque necessário para que a linha de produção não pare. No entanto, a falta de conhecimento ou sistemas de controle pode levar ao excesso, que ocupa espaço, aumenta custos e pode mascarar problemas no processo. Assim, ao reduzir os estoques, aparecem as falhas de entregas de material, não conformidades de produtos, paradas de linhas, entre outros.
A metodologia Lean como mudança de cultura, repensando todo o processo produtivo
Com o Lean, é possível repensar todo o processo produtivo e identificar onde estão os gargalos e as atividades que podem ser eliminadas ou melhoradas. Isso ajuda a empresa a trabalhar de forma mais eficiente, reduzindo custos e aumentando a qualidade dos produtos. Nesse sentido, é importante ressaltar que o Lean não é uma ferramenta, mas uma mudança de cultura que envolve todos os níveis da organização.
Estudo de caso: aplicando a metodologia Lean em uma empresa frigorífica
Certa vez, ao aplicar os conceitos de Lean em uma empresa frigorífica, foi possível identificar diversas atividades que geravam gargalos no processo produtivo. Para isso, utilizou-se uma metodologia de cronoanálise com foco Lean, analisando as atividades para reduzir e eliminar desperdícios.
1 – Análise e otimização das tarefas
Inicialmente, foi calculado o takt time (TT) do processo, que corresponde ao tempo disponível dividido pela demanda do cliente. Após esse cálculo e a coleta de dados no gemba (local onde as atividades ocorrem), foram identificadas ociosidades e sobrecargas entre os colaboradores. Essa avaliação só foi possível pois inserimos os dados coletados em um gráfico, que no lean chamamos de GBO (gráfico de balanceamento operacional). Com base na análise do GBO, foi possível readequar as atividades e redistribuir a mão de obra, promovendo um balanceamento das tarefas. Esse ajuste levou em conta o ritmo de produção, a segurança, a qualidade e a ergonomia no desempenho das atividades, assegurando que a demanda fosse atendida ao final do dia.
2 – Identificação de desperdícios e interrupções no processo de produção
Outro problema identificado foi a falta de etiquetas para a identificação dos produtos. Em determinados momentos, a linha de produção era interrompida devido à indisponibilidade desse material, que se encontrava somente no almoxarifado anexo a fábrica. Por outro lado, em algumas ocasiões, haviam sobras de etiquetas, o que gerava perdas financeiros desnecessárias.
Para agravar a situação, enquanto a estação de trabalho permanecia parada aguardando as etiquetas, os processos anteriores continuavam operando, resultando em acúmulo de produção nessa etapa. Essa dinâmica comprometia o fluxo contínuo e gerava estresse desnecessário na equipe, que, em alguns casos, precisava realizar horas extras para cumprir o volume de produção planejado.
3 – Solução – Implementação do conceito “supermercado” de embalagens e método Just in Time de abasteceimento
Para solucionar o problema, foi implementado o conceito de “supermercado” de embalagens, aliado a uma frequência regular de abastecimento. Esse sistema garantiu que as etiquetas estivessem sempre disponíveis na quantidade certa, no momento certo, atendendo às necessidades específicas daquela etapa do processo. Esse método, conhecido no Lean como Just in Time (JIT), busca sincronizar a disponibilidade de insumos com a demanda real, evitando atrasos e desperdícios.
O “supermercado”, por sua vez, consiste em um estoque controlado com níveis mínimos e máximos definidos para um insumo, localizado estrategicamente e abastecido de forma padronizada. Imagine o conceito de um supermercado: o produto está disponível para consumo imediato, mas com reposição frequente e organizada.
Resultados da aplicação do Lean Thinking
A aplicação dos conceitos Lean frequentemente resulta em ganhos significativos, como aumento de 20% na produtividade e eficiência, redução de 30% a 50% nas perdas e diminuição superior a 50% no tempo de setup (troca de ferramentas ou ajustes). Esses resultados, entretanto, dependem diretamente da dedicação da equipe e do suporte consistente da alta direção durante a implementação.
Aplicação do Lean Thinking na Minerva Foods
Um outro estudo de caso importante foi a aplicação do conceito de Lean Thinking por meio do Mapeamento Operacional na Minerva Foods, empresa brasileira de alimentos com sede em Barretos (SP).
“A implementação do projeto do Mapeamento Operacional (GBO) foi extremamente positiva para a Minerva, pois além da Capacitação dos profissionais selecionados para integrar a equipe, dentro de uma metodologia conceituada e muito aplicada no mercado, nos permitiu uma identificação muito clara do dimensionamento de recursos necessários, revelando oportunidades de melhorias que foram importantes para o direcionamento de projetos e ações objetivando o aumento da produtividade“, atesta Marcio Ratico, da Minerva Foods.
Ratico destaca ainda que “o resultado foi uma integração eficiente entre as diversas plantas/unidades e uma cultura organizacional voltada para a melhoria contínua e inovação, que é um dos nossos valores. Assim, o projeto não apenas impulsionou ações para melhoria da produtividade, mas também uma atmosfera de colaboração e aprendizado dentro da companhia”.
Sendo assim, seja no setor de alimentos ou em outros mercados, o Lean pode ser aplicado em qualquer lugar onde há processos, pois sua essência é identificar e eliminar desperdícios, sempre com o foco no cliente. Implementar essa filosofia pode ser o primeiro passo para transformar a empresa e garantir maior competitividade no mercado.